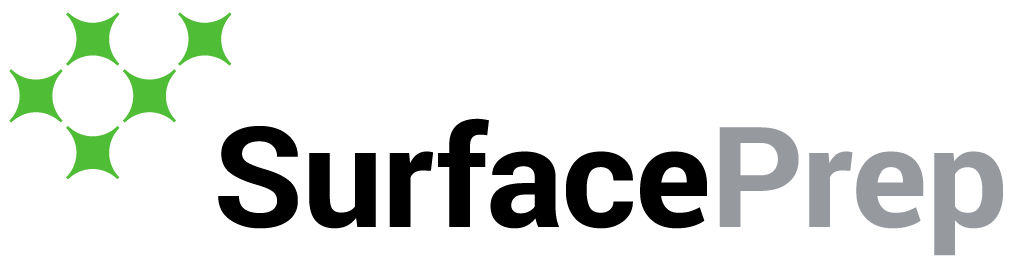
Comparing Suction and Pressure Manual Blast Cabinet Systems
Abrasive blasting is an essential process in the metal finishing industry, and choosing the right system can significantly improve your project's success. Let's break down the differences between suction and pressure abrasive air blasting cabinets to help you make an informed decision.
Suction Abrasive Blast Cabinets
Suction blast cabinets operate by using compressed air to create a vacuum
that draws abrasive media into the blast gun. These systems are identifiable
by two hoses connected to the gun—one for air and one for media. The air
and abrasive mix in the gun before being projected onto the workpiece.
Advantages
- Cost-Effective: They require a lower initial investment, use less air
volume (cfm), and consume less media. - Easy to Use: Their simple design means minimal training is required.
- Low Maintenance: With fewer parts, there's less wear and tear.
Ideal Applications
- Surface Cleaning: Effective for light rust, mill scale, and coating removal.
- Deburring: Great for smoothing edges and removing excess material.
- Surface Preparation: Suitable for creating a surface profile for finishing processes.
Pressure Abrasive Blast Cabinets
Pressure blast cabinets utilize a pressurized vessel where abrasive media is stored. Compressed air forces the media through a single hose and out the nozzle at high velocity, making them a more capable but typically more expensive alternative to suction blasting.
Advantages
- Productivity: Up to four times faster than suction systems, making them ideal for larger parts.
- Media Versatility: Effective with all types of media, including heavy media like steel shot and steel grit, as well as lightweight media like plastic and bicarbonate soda.
- Higher Media Velocity: More effective at removing durable coatings quickly.
Ideal Applications
- Surface Cleaning: Suitable for heavy rust, mill scale, and coating removal.
- Surface Preparation: Creating a surface profile for finishing processes.
- Coating Removal in Aerospace: Removing coatings for component inspections.
Making the Right Choice
When deciding between suction and pressure abrasive blasting systems, consider the following:
- Project Scope: Understand the size, complexity, and number of parts to be processed.
- Desired Result: Know the component material type and the substrate that needs to be removed.
- Production Rate: Determine how much throughput is needed to keep up with production demands.
Conclusion
Choosing the right abrasive blasting system is crucial for the success of your metal finishing projects. Suction systems are ideal for lighter surface preparation, requiring lower productivity and shorter blast cycles. They are affordable and easy to use. On the other hand, pressure systems are best for more demanding surface preparation, offering more versatility and higher productivity, though they come at a higher cost.
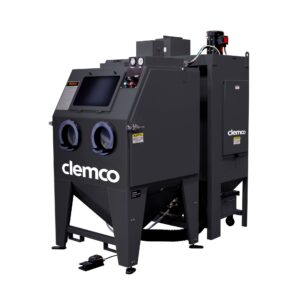