The Basics of Blast Nozzles: Factors to Improve Your Efficiency
Introduction
The blast nozzle is the final exit point for high-speed abrasive particles in an
air blast system and is a crucial component in achieving precise, efficient
surface preparation. Work is done in direct proportion to the volume and
pressure of air passing through the nozzle. Different nozzles wear at different
rates, and this wear is significantly affected by the nozzle material, the
compressed air sources PSI (Pounds per Square Inch), and CFM (Cubic
Feet per Minute). The nozzle orifice determines the work to be done, and the
size of the air compressor required. In this article, we’ll break down how
these factors combine to impact the lifespan of your blast nozzles.
The Role of Nozzle Material
Nozzle material is the most decisive factor in determining the lifespan of a
blast nozzle. Let’s dive into the most common materials used to manufacture
blast nozzles, and their typical lifespans:
Ceramic Nozzles
- Lifespan: Approximately 20-40 hours
- Characteristics: Cost-effective, but tend to wear out relatively quickly
- Ideal for smaller, intermittent projects.
Tungsten Carbide Nozzles
- Lifespan: Around 200-300 hours
- Characteristics: Wear-resistant, commonly used in industrial applications,
and moderately priced. These nozzles offer a balance between durability
and cost.
Silicon Carbide Nozzles
- Lifespan: Approximately 300-400 hours
- Characteristics: Very hard and exceptionally wear-resistant, lightweight,
and thermally stable. Perfect for heavy industrial use where longevity is
key.
Boron Carbide Nozzles
- Lifespan: About 700-1000 hours
- Characteristics: Extremely wear-resistant, and the most durable of
commonly used materials. Although they come at a higher price point,
their longevity often justifies the cost.
How PSI Affects Nozzle Lifespan
Increased PSI levels generally result in faster wear on your blast nozzles due
to the higher force of abrasives hitting the nozzle.
For example:
- At 90 PSI, a tungsten carbide nozzle might last up to 300 hours.
- Increase the pressure to 120 PSI, and the same nozzle might only last up
to 200 hours
The Role of CFM in Nozzle Wear
Higher CFM usually results in increased abrasive velocity, and consequently,
faster wear of the nozzle. The more volume of air and abrasive that passes
through, the quicker the nozzle wears.
For example:
- A tungsten carbide nozzle operating at 350 CFM might last around 300
hours. - The same nozzle operating at 450 CFM might last only around 200
hours.
Maximizing Nozzle Lifespan to get the most out of your blast nozzle.
- Operate at the lower, yet effective, PSI and CFM levels to reduce wear.
- Regularly inspect your nozzles for cracks or orifice wear as these could
lead to premature damage and ultimately failure of the nozzle. It’s best to
replace them before they wear out to the point of affecting your work or
damaging other components of your system. - Choose the right nozzle material for your application. Sometimes
investing in a more expensive nozzle saves money in the long run due to
its extended lifespan.
Why Choose SurfacePrep Nozzles
At SurfacePrep, we pride ourselves on offering a
comprehensive range of high-quality, durable
blast nozzles. Our expert team is always on
hand to advise on the best nozzle for your
specific needs and operating conditions. We
ensure you get the performance you need
without unnecessary wear and expense.
Conclusion
The lifespan of a blast nozzle in an abrasive air
blast system is significantly influenced by the
material of the nozzle and the operating
conditions, namely the PSI and CFM levels. By
understanding these factors and choosing a
nozzle based on your specific needs, you can
maximize efficiency, reduce costs, and maintain
the high-quality output that your projects
demand.
For the highest quality blast nozzles
and expert advice, contact
SurfacePrep today!
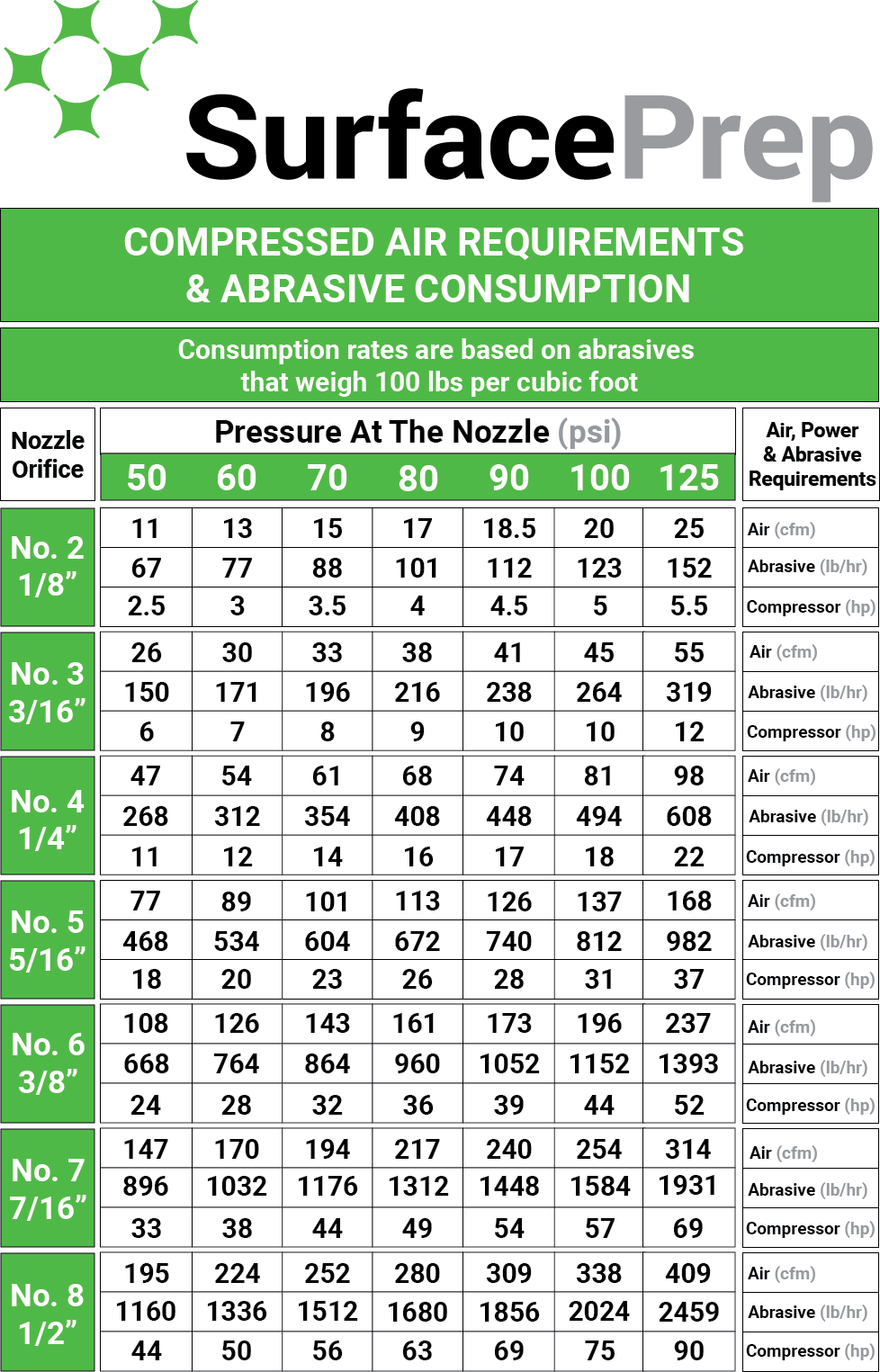