Choosing the Right Size of Steel Shot or Grit Blast Media
Understanding Steel Shot and Steel Grit
Steel Shot
Round and smooth, steel shot is perfect for many blast cleaning applications such as removing sand from foundry castings, scale from forged parts, rust from structural steel, as well as specialist applications such as shot peening to impart compressive strength to metal surfaces on parts such as aircraft engine turbine blades and airframes. The surface finish generated using steel shot depends on the size of shot being used and the hardness of the workpieces being processed. Shot is often used for cleaning and preparing component surfaces prior to paint coating.
Steel Grit
Angular and sharp-edged, steel grit is excellent for faster more aggressive cleaning, and is often used in air blast rooms where an operator directs a blast hose towards the parts being blast cleaned to remove paint, rust, and scale from metal surfaces. Depending on the size and hardness being used, steel grit provides an etched or roughened anchor pattern finish, which is great for strong adhesion of paint coatings. Often used in structural steel applications such as ship and rail car manufacturing due to its high recyclability (200 times) compared to non-recyclable abrasives (less than 5 times). Another significant advantage is its ability to be used at a lower air blasting pressure and still achieve a similar profile to other abrasives used at a higher pressure.
The Basics of Sizing
Steel shot and grit sizes range from fine to coarse, and the choice depends on your application. Sizes are typically categorized using a number, like S170 orG25. For steel shot, the 'S' refers to the shot, and for grit, the 'G' indicates grit. The following number signifies the size.
Application Based Sizing
Surface Cleaning
Light Cleaning: For removing light rust or a thin coat of paint, you'll want to go with a finer grit or shot, such as S170 or G50. These finer particles are less aggressive, preventing unnecessary surface damage while still generating an acceptable surface profile for coating applications.
Heavy Cleaning: For dense rust, multiple layers of paint, or scale, coarser grit likeG18 or G25 can be more effective. The aggressive nature of coarse grit ensures thorough cleaning but will generate a much rougher surface that will require more paint to completely cover the surface.
Shot Peening
Steel shot manufactured in special hardness ranges that meet either automotive or aerospace specifications are typically used for peening applications. The size of media is often called out on part drawings making it easier for the user to determine the correct product for their application.
Blast Cleaning for Surface Profile
Blast cleaning to create a surface texture on components prior to the application of coatings is the most common blast cleaning operation in the industry. Steel shot or a mixture of shot and grit is typically used in automated Blast Wheel Machines, while steel grit in smaller sizes is typically used in Air Blast Rooms to clean complex geometry parts with difficult-to-reach areas.
Equipment and Cost Consideration
The size and hardness of the abrasive media can also affect maintenance costs on blast equipment. Generally, steel shot generates less equipment wear than grit, translating to lower maintenance costs, but this is not always the case. Steel grit also comes in a standard hardness 40-50 HR C and has some cutting power but is less aggressive on blast equipment than a higher hardness 60 HR C plus steel grit which typically should only be used in air blast equipment due to the higher wear rate to machine components. It's a balance that needs to be evaluated based on project requirements.
Test Blasting Parts to Determine the Correct Media
We recommend utilizing our test labs located around the country to help find the ideal process to achieve the surface finish results you need. Our experienced lab technicians will use the best-suited media on your trial parts to generate the surface finish required. This will allow you to gauge the finish, speed, and potential equipment needed for your specific project without disrupting ongoing manufacturing production.
Conclusion
The right size of steel shot or grit blast media can make all the difference in a project's outcome. By understanding the application requirements and keeping in mind the equipment considerations, optimal results can be ensured. Always remember, the end goal is to achieve effective cleaning, surface profile, or peening results without causing unnecessary damage to the part surface or equipment.
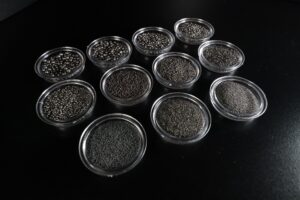