What is Shot Peening?
Shot peening is a controlled process used to finish metal parts to prevent fatigue and stress corrosion failures. Shot peening also helps prolong a product's lifespan.
Shot peening increases the life span of many components by removing residual tensile stress and applied tensile stress. The combination of residual and applied tensile stress increases fatigue rate (failure) and decreases fatigue life. Peening increases fatigue life by placing beneficial compressive stress into the component surface.
Residual tensile stress can be caused by:
- Turning
- Milling
- Drilling
- Boring
- Grinding
- Bending
- Decarburization
- Welding
- Anodizing
- Plating
- Corrosion
Applied tensile stress is created when an external force is applied to a component such as compression in springs and gear teeth.
Shot peening is a process used to produce a compressive residual stress layer and modify the mechanical properties of metals and composites. It entails striking a surface with shot using enough force to create sufficient deformation. It is a cold working process in which small spherical shot is blasted or propelled onto the surface of the part being finished.
Like a peen hammer used by blacksmiths to create a more durable product, the shot peens, or dimples, the surface causing small compression stresses. As the shot continues to dimple the surface, those dimples overlap continuously. Surface pores can also be closed during the peening process. This constant compression stress of the surface strengthens the metal, helping it resist fatigue failures, erosion and galling from cavitation and helps prevent corrosion and cracking.
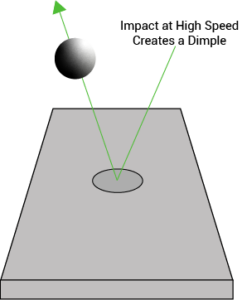
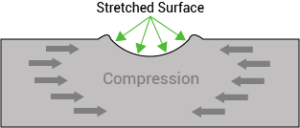
Why would you need to shot peen?
Surface treatment or manufacturing processes like grinding, brake bending or heat treatment procedures can cause tensile residual stress. This type of surface stress in parts lead to low life cycles.
Shot peening removes tensile residual stress which leads to a significant life cycle increase of the parts and strengthens their load capacities.
Shot peening is used across a variety of industries, such as medical, aerospace and automotive. Example workpieces include gear parts, springs, pistons, drill bits, turbine blades, orthopedic implants, and landing gear.
Different types of shot peening processes:
- Regular Shot Peening – Used to induce compressive stress in the surface of parts that are prone to repetitive loads and used to reduce stress and corrosion cracking.
- Shot Peen Forming – This is a process that compresses and extends the superficial surface layer of a part, causing it to bow and change shape. It is a purposeful bowing for applications such as the formation of wing flaps, access panels and fuselage sections.
What does the shot peening process look like?
Shot peening is commonly accomplished by using air blast systems or centrifugal wheels. Air blast systems use high pressure air to fire the rounded media at the workpiece. A centrifugal wheel, also known as wheel blast, propels the peening media by means of a rotating, bladed wheel onto a workpiece. Controls are used to give consistent media flow to ensure consistent and predictable coverage. Using automated or robotic equipment can help ensure an even, controlled surface and regulate the process so that each work piece, whether a turbine blade or spring, receives the same peening treatment. Most systems use shot classifiers to remove undersized, deformed and fractured media.
What media can be used for shot peening?
The most common media used would include cast steel shot, cut wire and ceramic or glass beads. Stainless steel cut wire, ceramic bead or glass bead should be considered when ferrous contamination of the surface cannot be tolerated.
How do you measure the effects of shot peening?
Intensity is a calculated value of how hard the surface of a part is hit when peening. The depth of the residual compressive stress is proportional to the calculated intensity value. Maintaining correct and consistent intensity ensures the layer of compression in the surface is the proper depth. Desired fatigue life improvements may not be obtained if the intensity is too low or too high.
The surface compressive stresses made during the peening process will differ depending on may factors such as the intensity and coverage of the media.
John Almen devised a way to measure the effect of shot peening. He created the Almen strip. The intensity of the shot peening stream can be measured in the deformation of the Almen strip. This is commonly referred to as arc height. An Almen gauge is used to read the arc height of an Almen strip measuring shot peening intensity. This is essential to ensure process consistency.
What is the effect of proper or improper coverage?
Coverage is the percentage of the peened surface that consists of indentations. The amount of coverage a part receives is dependent on the length of exposure to the media stream. Peening intensity is not affected by exposure time.
Incomplete coverage can cause premature fatigue failure by failing to remove or overcome the residual tensile stresses that can exist at the part surface from a previous shaping process, or it can fail to counteract and negate applied tensile stresses when the part is placed into service.
Shot Peening
Shot peening is a controlled process to assure the proper results and confirm consistency. Whether it is developing a proper shot peening process or following a documented peening spec requirement, SurfacePrep's shot peening specialists can help determine the proper course for your company.
SurfacePrep has many shot peening technical experts available to assist your company in shot peening processes. Whether you need assistance with improving an existing process or are looking to invest in shot peening for the first time, SurfacePrep is ready to help.