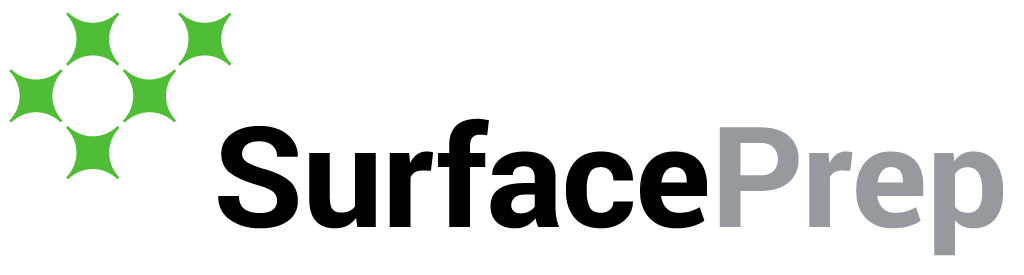
The Basics of Mass Finishing
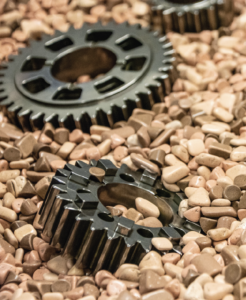
In the vast world of manufacturing, we often marvel at the sight of complex assembly lines or precision robotic arms. However, one crucial yet often unheralded step in the manufacturing process is 'finishing'. An area where Abrasive Mass Finishing truly shines.
Mass finishing is a set of manufacturing processes that concurrently clean, deburr, polish, and enhance the surface quality of multiple workpieces. This is accomplished by utilizing a range of equipment such as vibratory finishing machines, barrel tumblers, centrifugal disc machines, centrifugal barrel machines, and others. The use of abrasive media in these machines refines the aesthetic and functional properties of the products.
Vibratory finishing machines, for instance, leverage vibrations to cause friction between the parts and the abrasive media, effectively smoothing out surfaces. Barrel tumblers, on the other hand, rotate the parts and media together, achieving a similar outcome. For high-energy applications, centrifugal disc machines and centrifugal barrel machines are preferred, as they offer high speed and intensive finishing.
The primary advantage of mass finishing is its ability to efficiently process large volumes of parts, making it an economically viable solution for various industries, from automotive to aerospace, and even jewelry or medical technology.
The media used in abrasive mass finishing include ceramic media, plastic media, and natural media such as walnut shells or corn cob grit. The choice of media is contingent upon the specific requirements of the workpiece and the desired finish.
Mass finishing does come with its own set of challenges. Selecting the right machine-media-compound combo for specific parts can be intricate, and not all parts, especially those with delicate features or complex geometries, are suitable for mass finishing. The initial setup cost may be high, although it is often offset by reduced per-part processing costs and improved finished product quality.
At SurfacePrep, we have lab and R&D facilities to test and develop a custom tailored finishing process for your specific needs. Please visit our website surfaceprep.com to get connected to your local Solutions Specialist today.