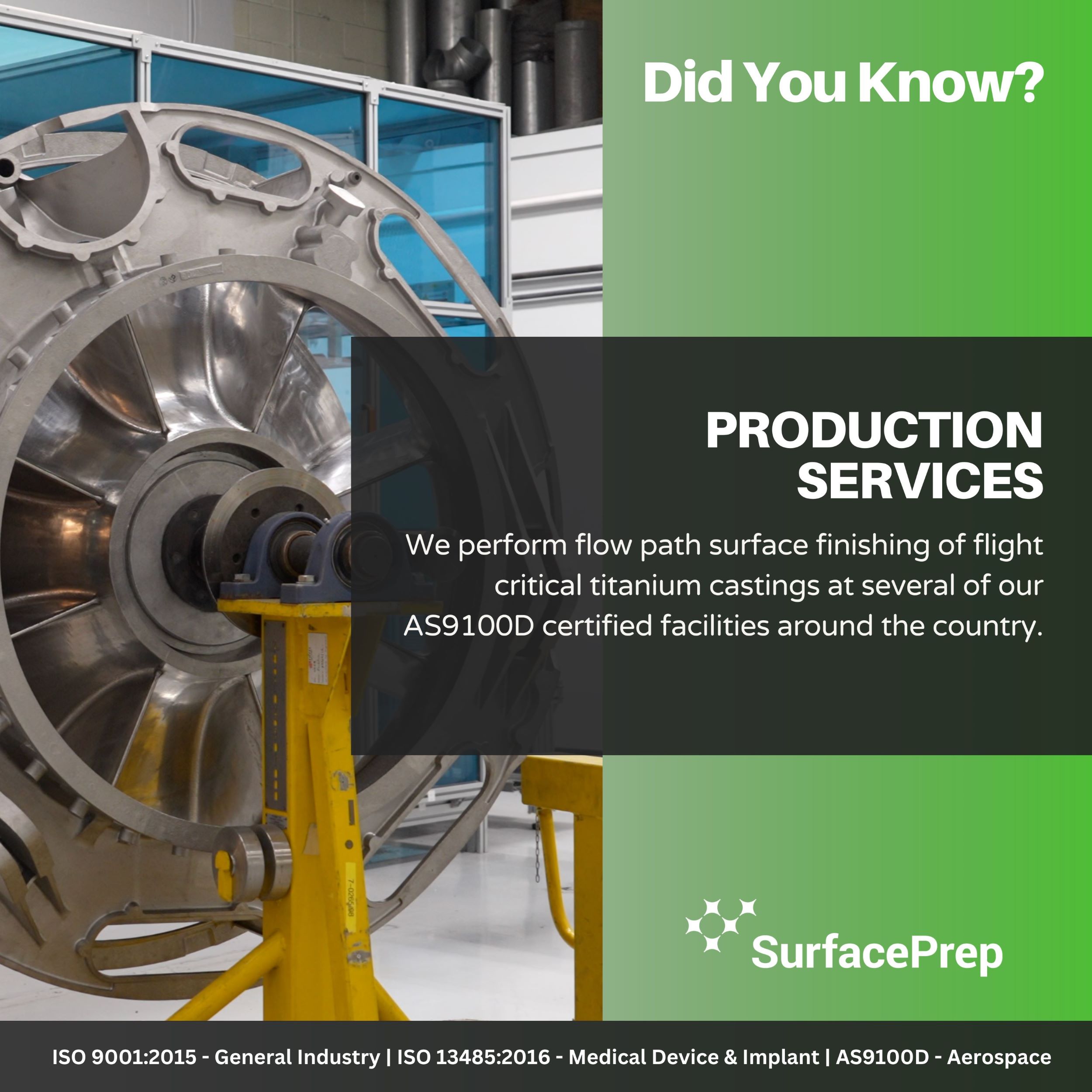
Surface finishing of cast titanium flow path channels is key to drag reduction and engine performance. At SurfacePrep Production Services division, we have mechanical finishing processes and systems dedicated to this task. In the event mechanical flow path finishing processes are not approved for a particular part number, we offer approved precision hand finish processing of these same features. AS9100D certified, our production facilities cater to stringent aerospace structural and rotating component requirements.
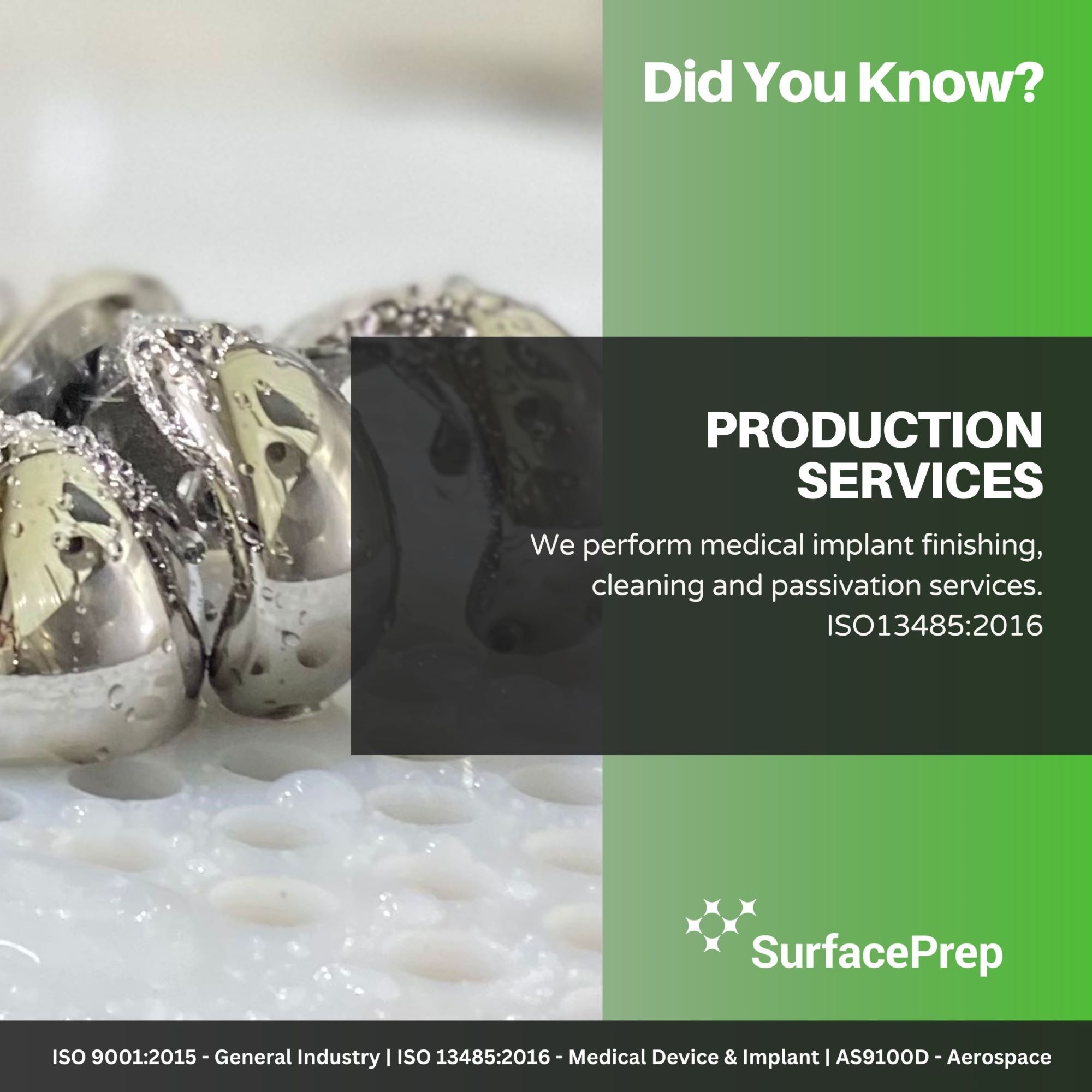
Orthopedic implants can have a wide range of surface finish requirements. Polished articulating surfaces are typical. Bone growth areas are often prepared via air blast with large grit aluminum oxides. Satin finished bone plates and other trauma components are often prepared with glass bead abrasives. Regardless of the surface finish requirement, via precision hand finishing, drag or other mass finishing methods, robotic belting or dry electropolish (DLyte), SurfacePrep’s ISO 13485:2016 certified production services are available to be your finishing department.
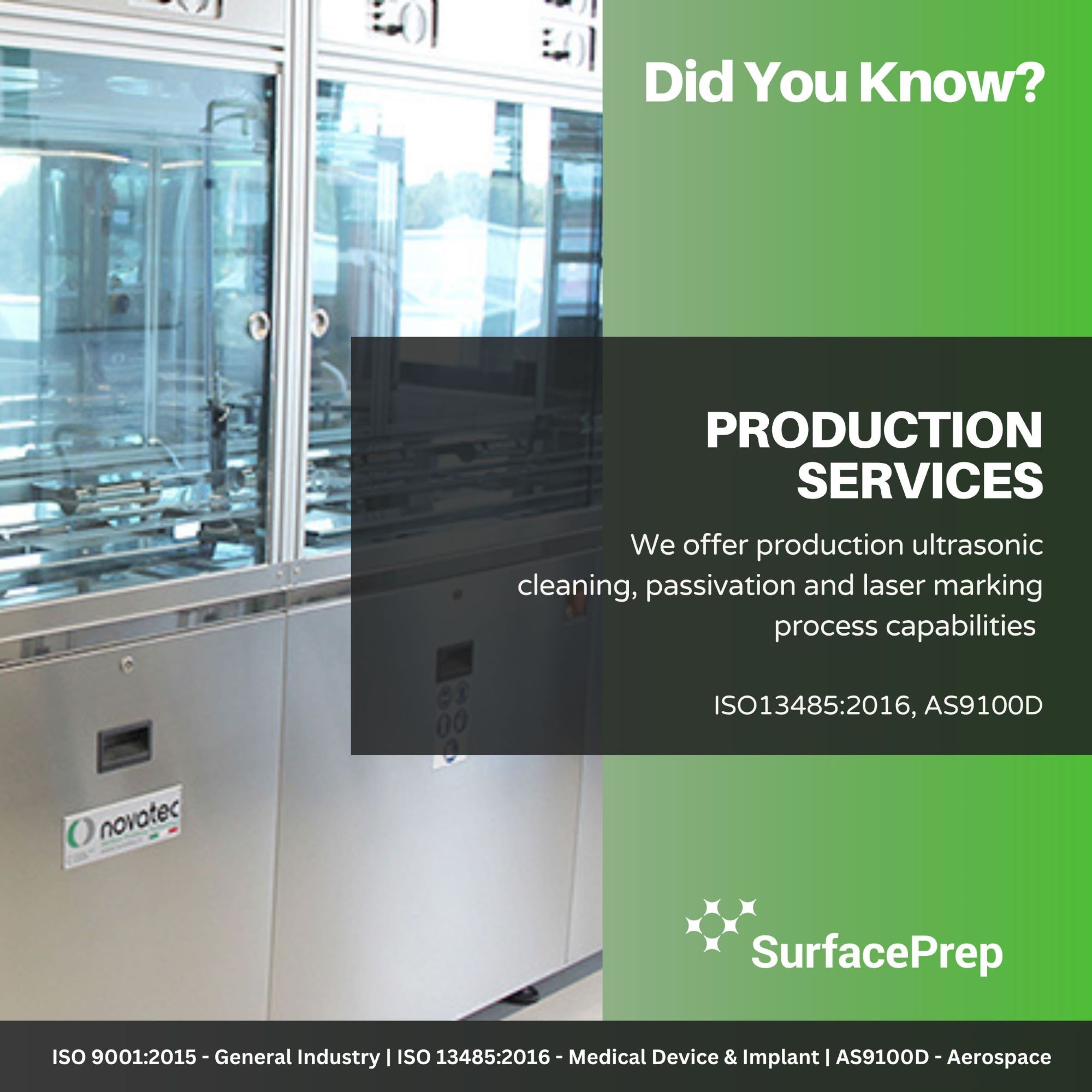
After surface finishing, ultrasonic or immersion cleaning and passivation typically follow.
Ultrasonic or immersion cleaning remove soils and particulate from the parts. Where some manufacturers do not allow use of ultrasonics on their parts, we also provide cleaning under vacuum which can intensify the cleaning process and drive access to tapped, blind holes or porous surfaces.
Passivation, whether citric or nitric based (see ASTM A967) works to remove free-iron that may have attached or imbedded in the finished surface. At SurfacePrep, we offer production cleaning (ultrasonic, immersion, vacuum) and laser marking services focused on the medical device and aerospace component industries. We are AS9100D, ISO13485:2016 Certified.
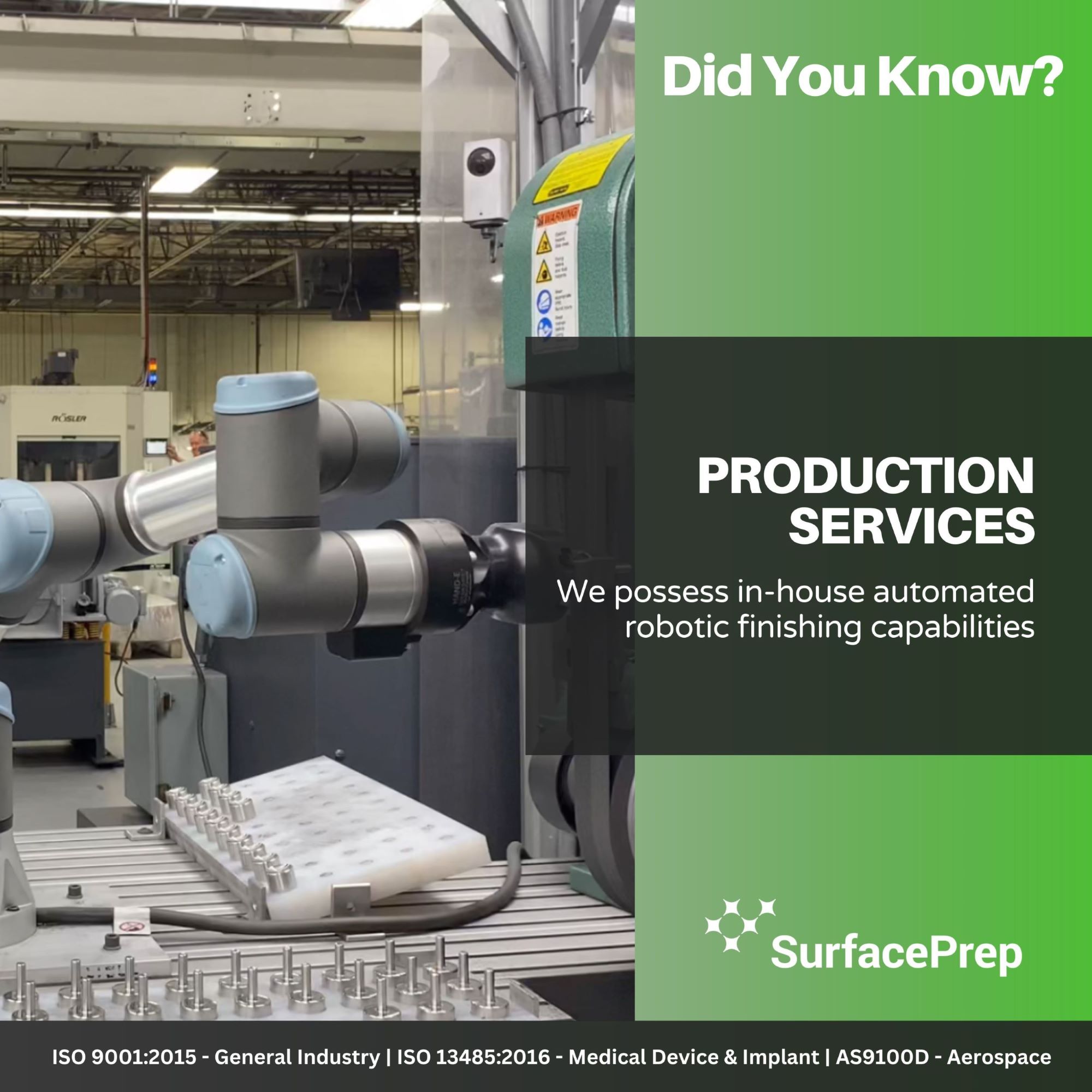
Production surface finishing via manual hand finishing techniques are often the most flexible methods. However, some components lend themselves to the opportunity for robotic automation. In these cases, SurfacePrep blends our manual process experience with our mechanical finishing expertise to create robust and repeatable automated finishing processes. Aerospace components and medical devices alike can benefit from this approach. Expert preparation, masking and post process cleaning are offered to complete the requirements. AS9100D, ISO13485:2016.